Protein skimmers in recirculation systems
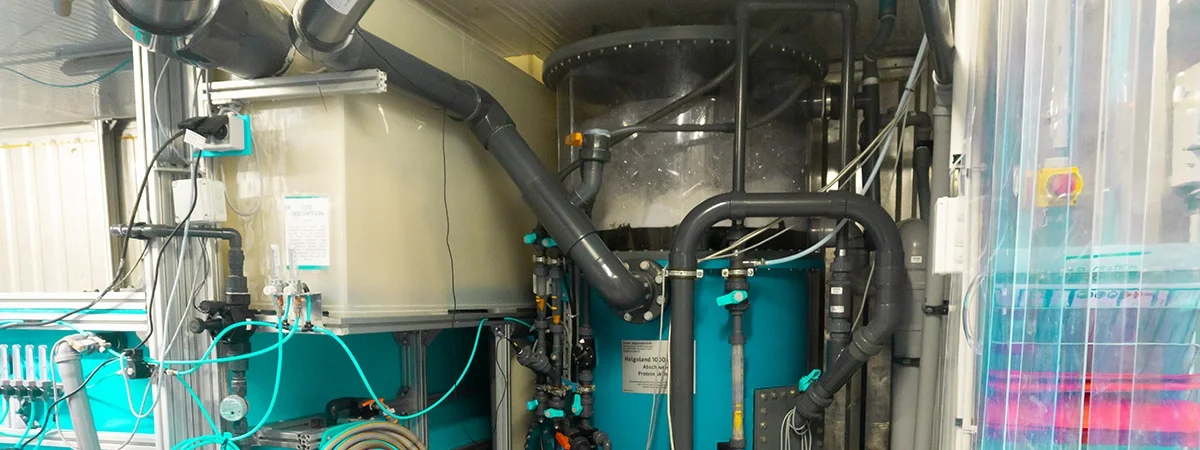
How does the skimmer work?
The skimmer uses the flotation process to remove smallest particles and bacteria. During flotation, very fine gas bubbles are introduced in the bottom area of the device. It applies that with higher salt content of the water finer gas bubbles are formed. Only from a salt content of about 1.2% the use of a skimmer makes economic sense. The advantage of finer gas bubbles is the comparatively larger reactive surface. Both these fine gas bubbles and the bacteria are electrically charged on their outer surfaces and therefore stick together. At the same time, the gas bubbles in the water of the reaction chamber rise upwards due to their buoyancy and thereby transport the attached particles. By tapering in the head area of the reaction chamber, the gas bubbles are collected at the water surface and a foam is created. This foam passes over the so-called foam pot, whereby the bacteria are removed from the water circuit together with the gas bubbles. The foam collects in a channel and collapses there over time. What remains is a sludge which is rinsed out as wastewater and thus contributes to the loss of water in recirculation systems.
The effect of flotation can be improved by adding ozone (O3). Ozone is produced as required in the so-called ozone generator. The demand is mainly based on the daily amount of feed. In the ozone generator ozone (O3) is produced from the oxygen (O2) in the ambient air by means of high-voltage electrodes and the resulting electrical discharge. The use of ozone supports the hygienization of the water in recirculation systems in two ways:
- Ozone is a very reactive substance and chemically breaks the bacterial shell, killing the bacteria.
- The substances from the inside of the bacteria lead to a better foam formation, whereby more particles can be removed at the same time.
During its reaction, the ozone decomposes back into oxygen so that no residual substances remain in the water.
Taste advantages through skimming
The installation of a skimmer in aquafarming systems brings not only clear water and the associated health aspects for the fish. It has also taste advantages for the end product. Fish farms – both in ponds and indoor systems – often have an off-flavor. This earthy, musty taste is caused by geosmin. Geosmin is produced by certain micro-organisms and is therefore often associated with turbid, particle- or bacteria-contaminated water. Fish with off-flavor are not particularly appealing in taste. The easiest way to remove the off-flavor is to keep the animals in separate tanks for several days or weeks, usually with a continuous high supply of fresh water and without the addition of food. A process which is very time- and resource-intensive and which hides the usually rather unfavorable living conditions. The use of a skimmer is therefore an attractive alternative.
Conclusion
In the SEAWATER Cube we use the ozone-supported skimmer technology, which removes not only bacteria but also geosmin. Fish always swim in clear, almost uncontaminated water and can therefore be taken directly from the production tank and processed without any advance planning or holding out. This reduces stress for the animals, saves working time and produces the tastiest possible end product. In addition, illnesses and the use of medication are completely avoided, providing the consumer with a higher quality food product and saving valuable raw materials such as energy and water. Through the combination with our biological filter processes, we achieve a total water recycling rate of 99%, so that only 1% (= 500 l) of wastewater is produced per day.
References:
— Image source: SEAWATER Cubes
— Wilhelm, S.: Wasseraufbereitung – Chemie und chemische Verfahrenstechnik. 7., aktualisierte und ergänzte Auflage; Springer-Verlag Berlin Heidelberg, 2008.
— Schwister, K.; Leven, V.: Verfahrenstechnik für Ingenieure. 2., aktualisierte Auflage; Carl Hanser Verlag München, 2014.
— Timmons, M., Guerdat T., Vinci B. (2018) “Recirculating Aquaculure”. Ithaca, NY.