Automation of fish farming systems
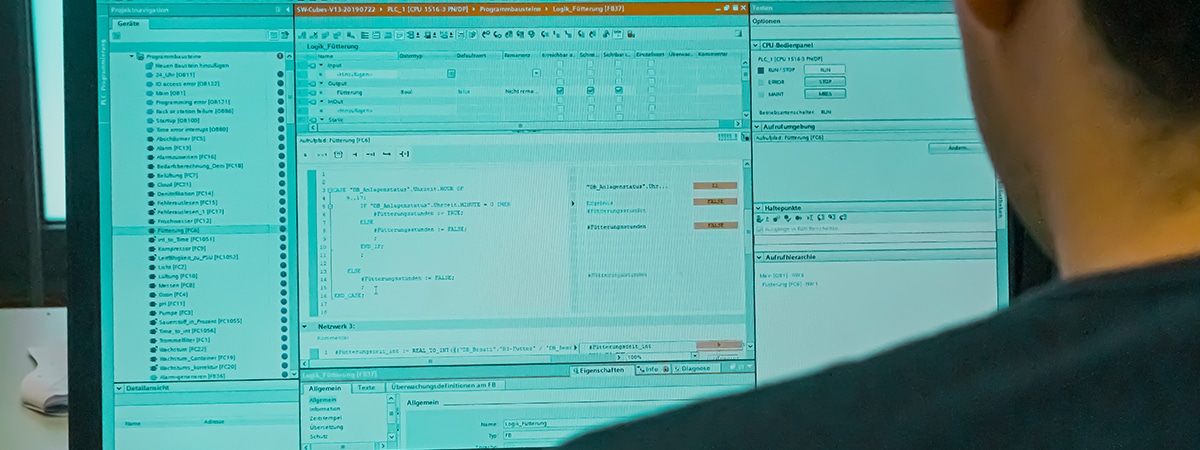
The topic of automation is becoming more and more important, especially in today’s world. Especially in industry, where high productivity is always the goal and processes are increasingly digitalized (Industry 4.0), many different applications of automation can be found. However, the beginnings of electrotechnical automation date back several decades. A major step was the development of the so-called programmable logic controller, or PLC, in the 1970s. Since then, this technology has been continuously developed to take over more and more tasks. Nowadays, the planning and implementation of electrotechnical plants is virtually impossible without such a PLC.
The programmable logic controller (PLC)
A programmable logic controller is basically the brain of a technical system. Its task is to ensure the optimal function of the respective plant. Decisive for its use are durability and reliability under difficult conditions. This means that the PLC is not affected by dust, corrosion or heat and the plant can therefore operate without constant supervision.
The application possibilities of a PLC are very wide. The desired functions, which the PLC is to implement, are programmed accordingly and loaded into the memory. During operation, input signals are acquired and processed according to the programming, and then output signals are issued to control other components. In addition to simple applications, highly complex tasks can also be implemented, making it highly versatile. Despite this, processing times are only in the millisecond range, which allows a fast reaction to occurring events.
In addition to controlling normal operation, the PLC is also used for general monitoring and detecting errors. If a fault should occur, it is detected directly and reported to the user via various warning systems and with detailed information, so that quick action or countermeasures can be taken. Such messages are output in the so-called HMI, the „Human Machine Interface“. This is a display that is connected to the PLC. In addition to the display of messages, it can also be used to control individual parts of the plant and to monitor various parameters.
Automation of recirculation systems
Programmable logic controllers are also increasingly being used in recirculation systems. In closed recirculation systems, many different parameters have to be controlled to ensure good water quality. This is essential for the well-being and health of the animals and thus for successful production. The following sensors are used to measure parameters in aquacultures:
The sensors regularly record measured values and forward them to the PLC. The system then reacts automatically to fluctuations and creates progression curves that can be viewed by the system operator. The following sensors are installed to measure parameters in aquaculture:
-
- temperature
- filling level
- ORP / redox
- PSU / salinity
- pH
- oxygen saturation (O2)
- flow rate
- carbon dioxide (CO2)
In addition to setting the parameters, the PLC is also responsible for controlling all actuators and subsystems. The following components can be connected to the automation:
-
- pumps
- compressor
- valves
- drum filter
- denitrification
- ozone generator
- sedimentation
- automatic feeder
- oxygen production
- light
- ventilation
State of the art aquaculture facilities are often equipped with software solutions for subsections or individual units (e.g. only for the drum filter), but do not have automation of the complete process. Therefore, the data consistency of coupled processes is not given, and the workload is difficult to generalize.
The fully automated SEAWATER Cube
For the SEAWATER Cube we have developed our own automation solution according to modern standards. This is based on Siemens technology and has more than 30 functions (e.g. feeding, rinsing, aeration) and thus controls about 20 subsystems, resulting in full automation of the entire process. The fish knowledge that is necessary for a smooth plant operation is stored in our control system. Thus, the operator does not necessarily have to be a biologist or fish farmer to control the rearing process. The plant knows all important directional limits and warning values and is able to react independently to changing conditions. In case of problems, the system calls the operator and the control system can also be accessed from outside via remote maintenance. The full automation also results in a plannable workload in plant operation of 1h per day on average. A cloud connection enables external access to all data of relevant process variables.
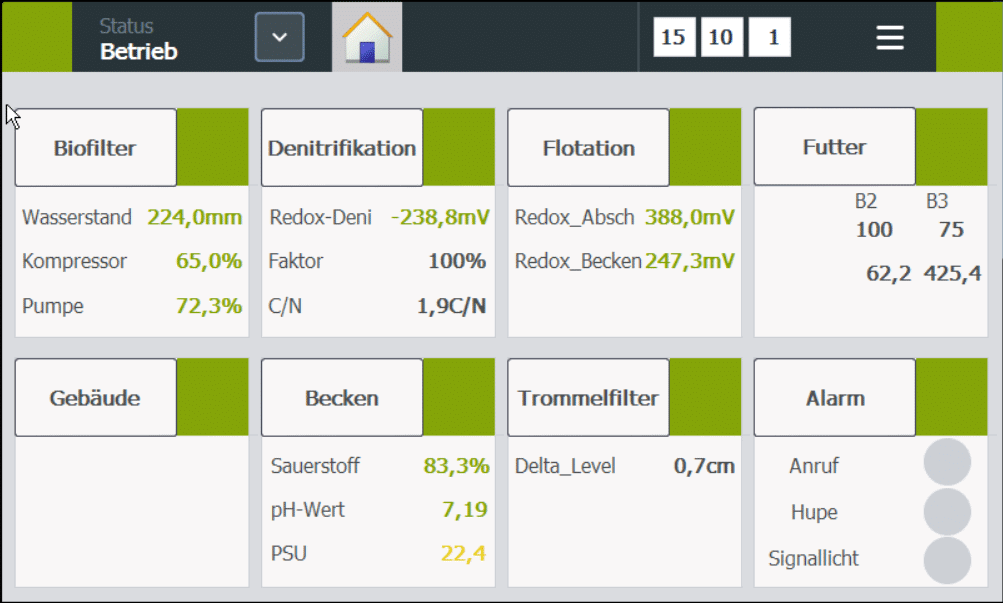
The panel as it is displayed in the SEAWATER Cube. Here you can see the overview page on which all relevant components are listed. There are different ways to get to submenus and to see and control more details.
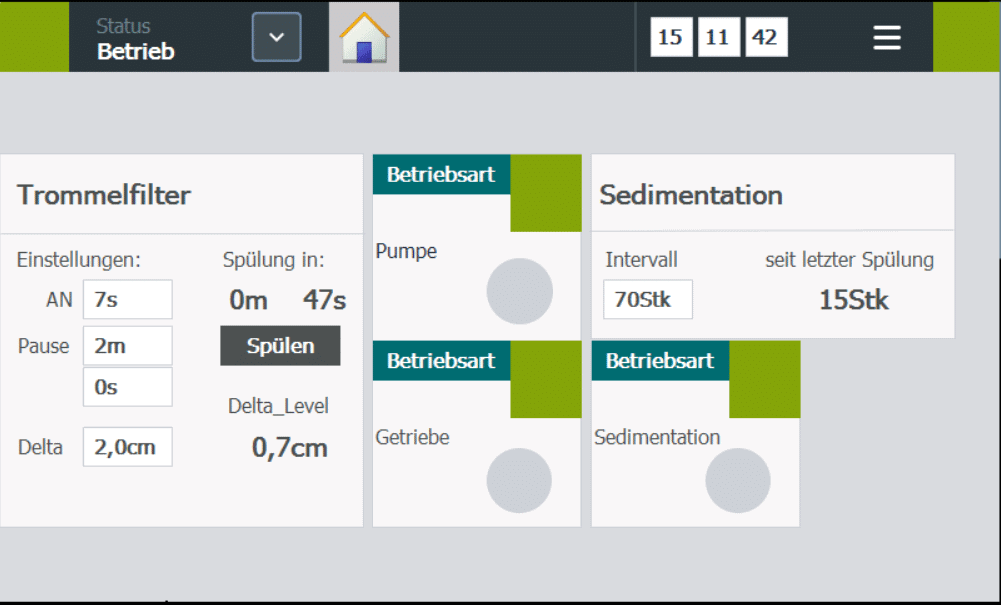
A control menu can be seen in this view, here on the drum filter as an example. The „Operating mode“ fields can be used to switch partial functions from automatic to manual mode.
In summary, the SEAWATER Cube uses modern automation technology through the use of a programmable logic controller to ensure optimal plant operation with a manageable workload. The state of the art in fish farming is thus raised to a new level.
References:
— https://www.elektrotechnik.vogel.de/was-ist-eine-sps-definition-grundlagen-und-funktion-a-773404/, 12.06.2020
— https://www.it-production.com/automation-und-robotik/hmi-scada-digitale-fischzucht/, 12.06.2020
— https://www.thuenen.de/de/fi/arbeitsbereiche/aquakultur/wirtschaftlichkeit-von-aquakulturen/, 12.06.2020